Thorough Welding Inspection Service for High-Performance Welding
Discover the Advantages of Different Types of Welding Services for Your Company

In the world of industrial operations, the option of welding solutions plays a pivotal duty in establishing the high quality and efficiency of your business processes. Each welding strategy, from MIG to TIG, Arc, and Area welding, provides unique advantages that satisfy specific demands and demands. Understanding the nuances of these welding methods and exactly how they line up with your organization purposes can substantially influence your profits and operational success. As you navigate the detailed landscape of welding services, uncovering the one-of-a-kind benefits they give the table becomes not simply an option however a critical crucial for your company growth and competitiveness.
MIG Welding Benefits
MIG welding, likewise understood as Gas Steel Arc Welding (GMAW), supplies various advantages to companies looking for premium and reliable welding solutions. One main advantage of MIG welding is its convenience in dealing with different kinds of metals, consisting of stainless steel, light weight aluminum, and light steel. This versatility makes MIG welding a preferred choice for markets with varied welding needs.

Additionally, MIG welding is an affordable alternative because of its efficient usage of consumables such as filler material and protecting gas. This effectiveness translates to cost savings for businesses in the long run. Overall, MIG welding's combination of adaptability, rate, simplicity of use, and cost-effectiveness makes it a recommended selection for numerous welding applications.
TIG Welding Benefits
Tungsten Inert Gas (TIG) welding supplies exact control and extraordinary high quality in welding services for businesses calling for thorough and high-standard welds - Welding Inspection Service. TIG welding attracts attention for its ability to produce accurate and clean welds without spatter or triggers, making it suitable for applications where visual appeals and accuracy are paramount. One of the crucial advantages of TIG welding is its adaptability in welding various kinds of steels, including stainless-steel, aluminum, copper, and unique metals, offering businesses with a flexible welding remedy for different tasks
Additionally, TIG welding allows welders to function with thinner products efficiently, as the process enables reduced heat input and much better control over the welding arc. This leads to marginal distortion and a narrow heat-affected area, important for welding jobs where maintaining the architectural stability of the base products is vital. Furthermore, TIG welding generates premium, visually appealing welds that often need very little post-weld cleanup, conserving businesses time and resources. Generally, the specific control, top quality welds, and flexibility make TIG welding a preferred choice for companies seeking to achieve first-class welding outcomes.
Arc Welding Pros
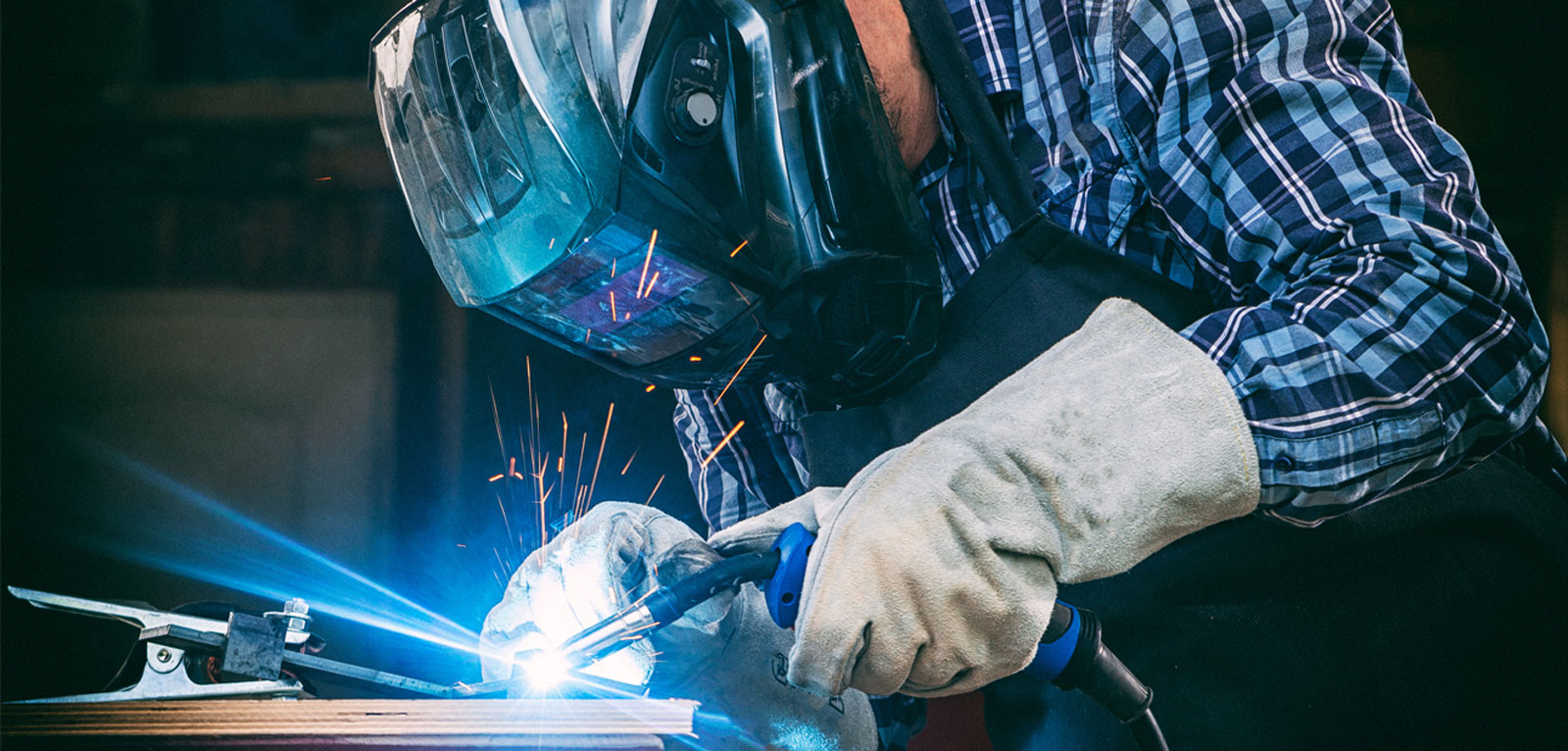
Spot Welding Conveniences
Area welding supplies countless benefits for businesses seeking precise and effective signing up with of steel parts in their production procedures. This welding method is highly economical because of its fast implementation, marginal requirement for comprehensive prep work, and lower power consumption contrasted to various other welding methods (Welding Inspection Service). Place welding also offers a tidy and neat surface, making it suitable for applications where looks are important
Among the vital advantages of spot welding is its capability to produce durable and solid bonds between metal surface areas. The process creates a focused warmth resource, resulting in a localized weld that lessens damages to the bordering locations. This concentrated warm application also reduces the danger of bending or distortion in the bonded products, guaranteeing the stability of the end product.
Furthermore, spot welding is very versatile and can be made use of on a wide variety of metals and alloys, including copper, steel, and aluminum. Its adaptability makes it a popular choice for sectors such as automobile, electronic devices, and aerospace, where accuracy and efficiency are extremely important. On the whole, the advantages of place welding make it a valuable asset for businesses seeking to improve their manufacturing abilities.
Welding Service Option Factors
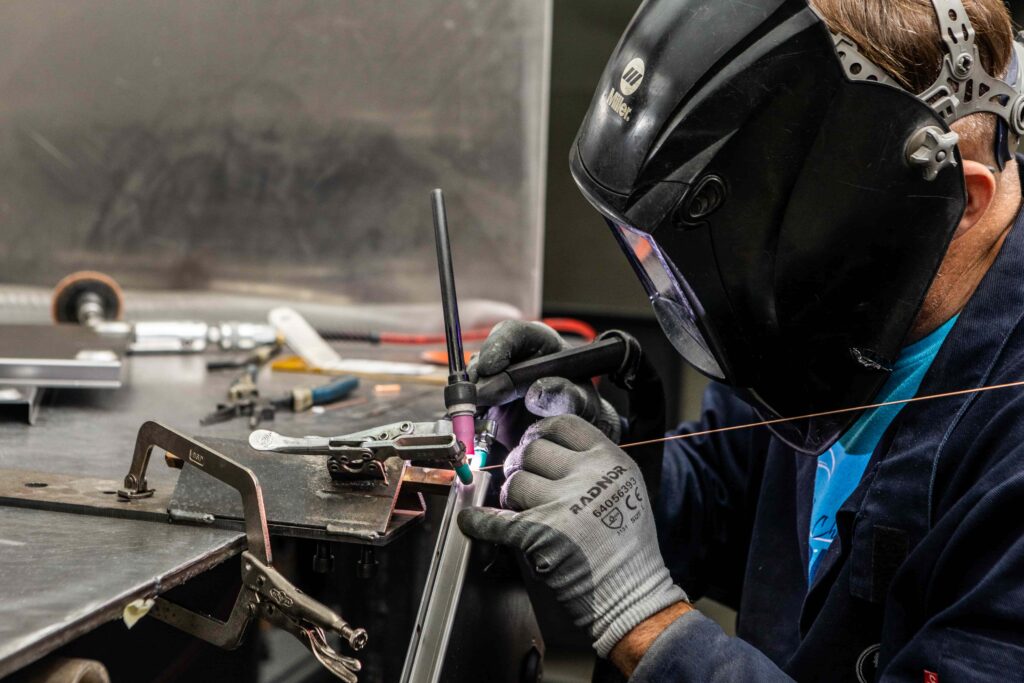
Another important link element to take right into account is the size and intricacy of the parts being bonded. Some welding techniques are better fit for detailed and small-scale jobs, while others are more efficient for bigger and a lot more simple frameworks. Consider the speed and efficiency of the welding his comment is here process. Depending on your production requirements, choosing a welding solution that can satisfy your timeline and result needs is essential for preserving performance. Finally, evaluate the cost-effectiveness of different welding solutions to ensure that you are obtaining the most effective value for your investment. By carefully thinking about these factors, you can select the most ideal welding solution for your company needs.
Conclusion
In conclusion, understanding the advantages of various types of welding solutions can considerably profit services in their decision-making procedure. MIG welding provides efficiency and rate, TIG welding offers high accuracy and clean welds, arc welding is economical and versatile, and spot welding is excellent for signing up with thin products. By taking into consideration these variables, companies can select one of the most appropriate welding solution to fulfill their specific demands and demands.
MIG welding, additionally known as Gas Metal Arc Welding (GMAW), uses countless benefits to services looking for premium and effective welding services. One of the key advantages of TIG welding is its flexibility in welding different kinds of steels, consisting of stainless steel, aluminum, copper, and exotic metals, offering businesses with a flexible welding solution for numerous jobs.
Arc welding is understood for its high welding rate, allowing efficient completion of welding jobs (Welding Inspection Service). In general, the pros of arc welding make it a valuable welding solution for companies looking for a flexible, affordable, and reliable click this welding service
MIG welding uses efficiency and rate, TIG welding offers high accuracy and clean welds, arc welding is flexible and cost-effective, and area welding is ideal for joining thin products.