Welding WPS for Beginners: Getting Started with Welding Treatment Requirements
Unlocking the Power of Welding WPS: Strategies for Performance and Safety in Manufacture
In the world of construction, Welding Procedure Requirements (WPS) stand as the foundation of welding operations, determining the essential actions for achieving both effectiveness and safety and security in the manufacture procedure. Comprehending the complexities of WPS is extremely important to utilizing its complete potential, yet many companies struggle to unlock the real power that lies within these records (welding WPS). By delving into the strategies that maximize welding WPS, a world of improved productivity and increased safety awaits those going to check out the subtleties of this crucial aspect of construction

Relevance of Welding WPS
The significance of Welding Procedure Specs (WPS) in the manufacture sector can not be overemphasized. WPS act as an essential roadmap that lays out the essential steps to ensure welds are done consistently and appropriately. By defining necessary criteria such as welding processes, materials, joint layouts, preheat temperature levels, interpass temperatures, filler metals, and post-weld warm therapy needs, WPS provide a standardized approach to welding that improves effectiveness, high quality, and safety in construction processes.
Adherence to WPS aids in attaining harmony in weld top quality, minimizing the probability of issues or architectural failings. This standardization additionally assists in compliance with market guidelines and codes, making certain that fabricated frameworks satisfy the needed security requirements. In addition, WPS documents allows welders to duplicate successful welding procedures, bring about regular outcomes throughout various jobs.
In significance, the meticulous advancement and rigorous adherence to Welding Treatment Specifications are vital for supporting the integrity of bonded structures, guarding versus prospective risks, and supporting the track record of manufacture companies for delivering high-quality items and solutions.
Secret Elements of Welding WPS
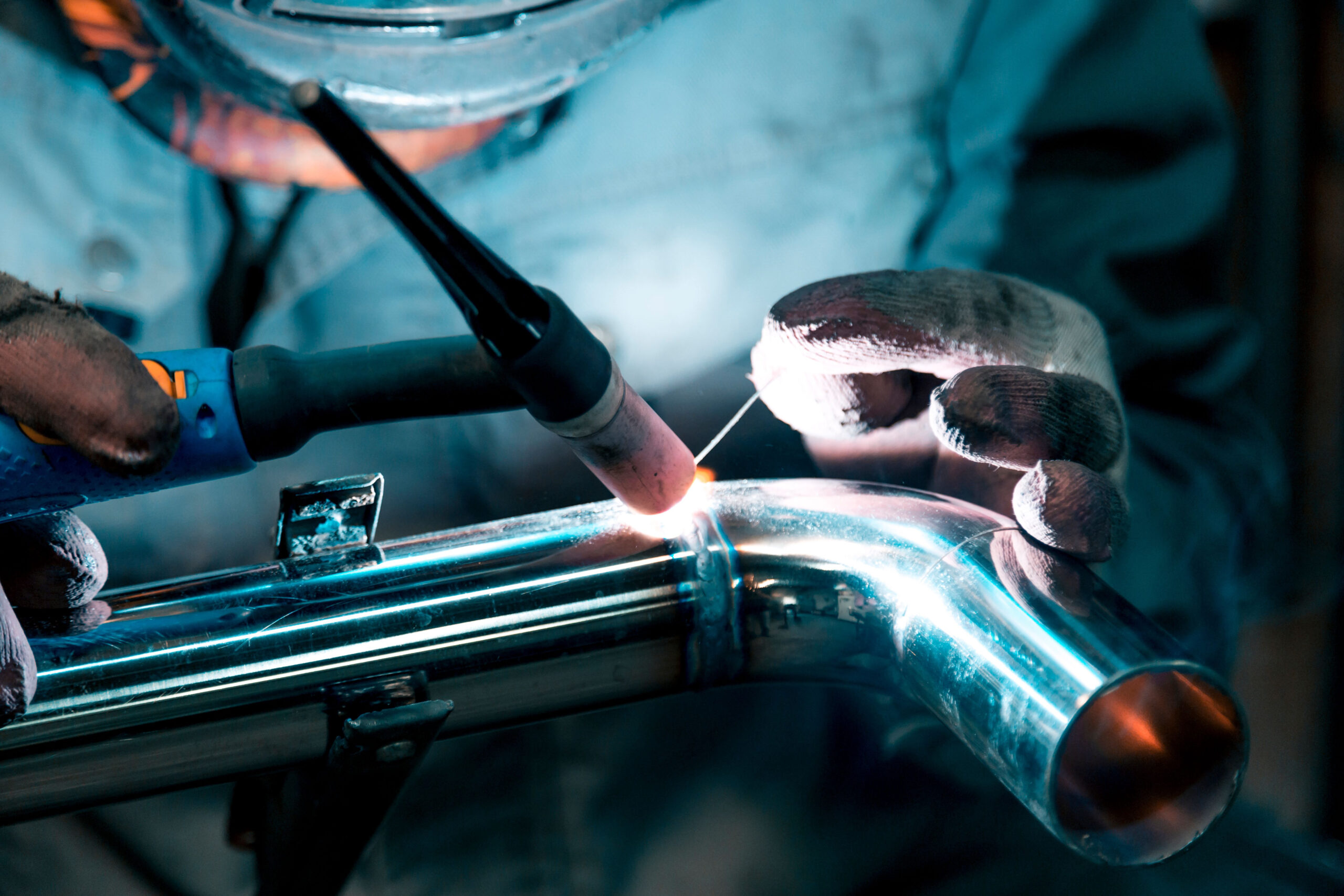
Enhancing Efficiency With WPS
When optimizing welding operations, leveraging the essential components detailed in Welding Procedure Specifications (WPS) becomes vital for optimizing and improving procedures efficiency. One way to boost efficiency with click for source WPS is by website here thoroughly selecting the appropriate welding parameters.
Furthermore, proper training and qualification of welders in understanding and carrying out WPS can even more boost effectiveness. Making certain that all employee are fluent in translating and performing the WPS accurately can rework and decrease errors, conserving both time and resources. Routinely reviewing and upgrading the WPS to integrate any type of lessons learned or technological innovations can also add to efficiency enhancements in welding procedures. By welcoming the standards stated in the WPS and continuously looking for ways to enhance procedures, fabricators can attain greater effectiveness degrees and exceptional end outcomes.
Ensuring Safety in Construction
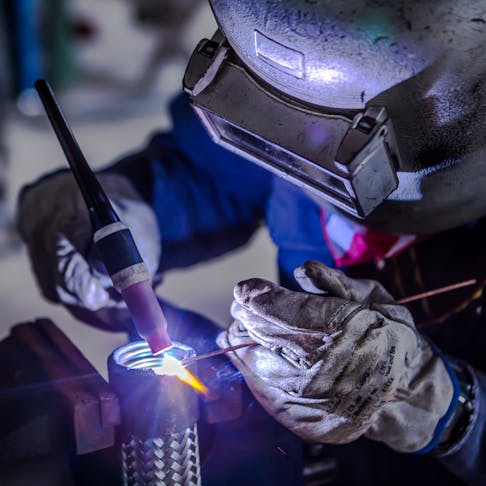
Making sure safety in manufacture includes a multifaceted technique that encompasses numerous elements of the welding process. Welders have to be equipped with suitable gear such as safety helmets, gloves, and protective clothes to alleviate dangers associated with welding tasks.
Moreover, adherence to appropriate ventilation and fume removal systems is critical in keeping a healthy work setting. Welding fumes consist of damaging materials that, if inhaled, can posture serious wellness risks. Applying effective air flow measures aids to decrease direct exposure to find here these unsafe fumes, promoting breathing health and wellness amongst employees.
Normal equipment upkeep and inspections are likewise crucial for making sure safety and security in manufacture. Faulty machinery can result in crashes and injuries, underscoring the significance of prompt repair work and regular checks. By focusing on safety procedures and cultivating a culture of understanding, manufacture centers can produce a efficient and safe workplace for their workers.
Applying WPS Ideal Practices
To improve operational efficiency and ensure top quality end results in manufacture procedures, incorporating Welding Procedure Specification (WPS) finest methods is vital - welding WPS. Carrying out WPS finest practices entails precise planning, adherence to industry requirements, and continual surveillance to ensure optimum outcomes. First of all, choosing the ideal welding process, filler material, and preheat temperature level defined in the WPS is crucial for achieving the wanted weld top quality. Secondly, guaranteeing that qualified welders with the necessary accreditations execute the welding treatments according to the WPS guidelines is necessary for uniformity and reliability. Consistently evaluating and upgrading WPS records to mirror any kind of process renovations or changes in products is likewise a crucial ideal technique to maintain accuracy and relevance. Additionally, offering thorough training to welding personnel on WPS requirements and finest methods promotes a society of safety and top quality within the manufacture atmosphere. By diligently applying WPS ideal practices, fabricators can improve their procedures, decrease errors, and supply remarkable products to fulfill client assumptions.
Conclusion
In final thought, welding WPS plays a critical duty in guaranteeing efficiency and safety and security in manufacture procedures. By adhering to these approaches, businesses can unlock the complete capacity of welding WPS in their fabrication operations.
In the realm of manufacture, Welding Treatment Requirements (WPS) stand as the foundation of welding operations, dictating the essential actions for attaining both effectiveness and safety and security in the manufacture process. By specifying necessary criteria such as welding processes, products, joint styles, preheat temperature levels, interpass temperatures, filler steels, and post-weld warm therapy needs, WPS give a standard approach to welding that improves performance, quality, and security in manufacture procedures.
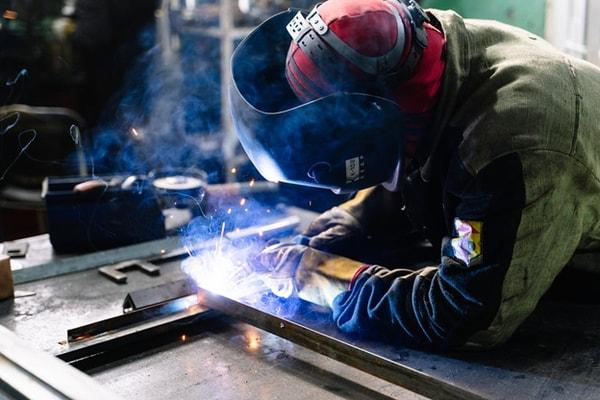
When maximizing welding procedures, leveraging the crucial elements outlined in Welding Procedure Requirements (WPS) comes to be vital for simplifying processes and optimizing efficiency. (welding WPS)